Projects
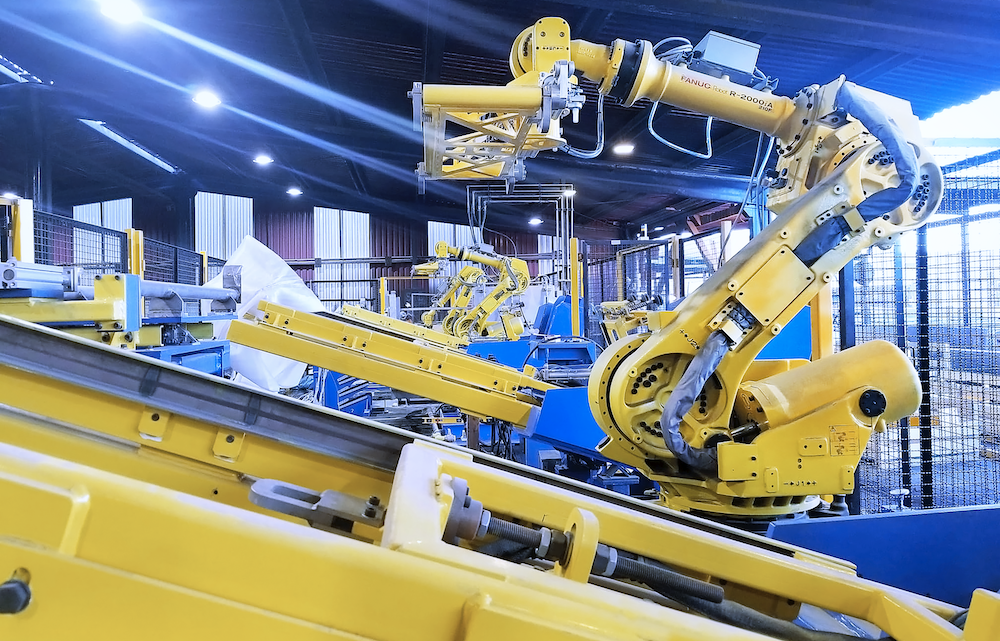
Implementing AI at Codelco revolutionizes mine with copper sorting machine
Client
As the world’s largest copper producer, Codelco produces 1.7 million tons of fine copper per year. Headquartered in Chile, Codelco explores, develops, extracts and processes mineral resources that are converted into refined copper and by-products. The Radomiro Tomic Mine in Calama, Chile produces high grades of copper sold on the global market.
Challenge
With Codelco’s strict quality standards in place, it was critical for our client to ensure high-grade copper cathodes were correctly separated from the off-grade product. The client had previously installed an automated copper cathode sorting machine system with little success. Like most automated sorting systems on the market, it required programming of complex algorithms to sort copper. However, each time a new defect arose, the algorithms had to be rewritten – a complicated, time-consuming, and expensive process.
As a result, Codelco decided to revert to sorting their production manually, with individual operators inspecting the quality of each cathode. But each person did the job a little differently based on their individual perceptions and judgments – which led to a lack of consistency in the sorting process.
Codelco was determined to find a new approach to overcome these challenges. In 2020, Codelco engaged EPCM and our Tecnologias COBRA division to develop an innovative solution that was both cost-effective and reliable. The goal of the project was to reach a 95% effectiveness level in sorting copper cathodes into the correct grade categories.
Solution
Prior to this project, Codelco had retained us to implement a materials handling system that automated the physical sorting of copper. However, we knew our client had a strong desire to automate the entire process from start to finish.
With this knowledge, we designed a fully automated solution that blended a deep learning vision system with our programming and integration capabilities. The Artificial Intelligence (AI)-based vision system operates by learning the characteristics of both high-grade and off-quality product, and then sorts accordingly – eliminating operator inconsistency.
But before implementing our solution at the facility, we wanted to be sure it would perform successfully. So we pilot tested the solution first, to prove out the concept. We decided to invest in and install the system on our own copper sort cell to measure its effectiveness.
The test was highly successful, delivering the results we’d hoped for. We now had proof of its capability that we could stand behind 100%. We began initial development for the vision system in the fall of 2020.
Outcome
Prior to engaging EPCM and COBRA, the client lacked confidence in the accuracy of their sorting process. However, with the implementation of our AI solution, our goal of 95% effectiveness was achieved. In fact, the results have been so impressive that we’re now installing a second automated vision system at the client’s facility.
EPCM’s vision system is the first step in making industry 4.0 practices a reality for base metal tankhouses globally. The system’s ability not only to sort grades of copper but to use this information in real-time to identify poorly performing cathode blanks and anodes of cells will enable our clients to quickly correct the root cause of issues. Its true power to provide KPI’s on cathode blanks and cell operations are only beginning to be fully harnessed in the industry.
In mineral processing, AI can be used to drive significant improvements in a number of applications including cathode verticality, hanger bar straightness, edge-strip verification and more.
But its potential for improving operational performance doesn’t end there. It extends across industries, to any environment that requires a human eye for inspection, and where traditional machine vision can’t solve the challenge at hand.
At The EPCM Group, we specialize in solving our clients’ most difficult operational challenges with single-source, life-cycle solutions. For over 40 years we’ve helped industry leaders around the world with integrated solutions including engineering consulting, automation, spare parts, supply, and service.
Contact us to learn how we can help you streamline processes and boost your bottom line with our end-to-end solutions.